SensorConnect can be used to quickly retrofit existing production lines and enrich the Unified Namespace with real-time data about running processes and the condition of machines. It is ideal for:
- Older Machines: For machines without connectable hardware to read relevant information, SensorConnect allows you to gather required data by placing third-party sensors (e.g., distance, vibration, inductive sensors) on the machine.
- Hybrid Setups: In cases where the existing machine PLC does not provide enough data, you can retrofit additional sensors or a button bar so that the operator can enter stop reasons.
Features
SensorConnect provides the following features:
- Supports connection to ifm IO-Link Masters such as the AL1350, enabling data acquisition from connected IO-Link devices.
- Works with all IO-Link devices that provide their data in the “process input data”. This includes a wide range of sensors and actuators compliant with the IO-Link standard.
- Using converters such as the DP2200 also sensors from 10 to 30V DC, producing binary outputs of true or false, and analog sensors with a current range spanning from 4 to 20 mA. can be connected
- Automatically downloads, caches, and interprets IO Device Description (IODD) files, converting raw hex-encoded sensor outputs into meaningful, human-readable JSON data.
- Continuously sends sensor information into the Unified Namespace
- Part of the open-source benthos-umh project
- When used with the the UMH, sensor data is accessible via the Tag Browser for real-time monitoring and analysis, as well as stored and visualized using the Historian
- Provides detailed metadata for each sensor reading, including port numbers, device IDs, product names, and more.
- Can be used with UMH Protocol Converters for standardized outputs or customized when using benthos-umh directly.
- Based on one of our oldest microservices, SensorConnect is already battle-tested.

What is IO-Link and ifm IO-Link Masters?
IO-Link is an industrial communication protocol used for integrating intelligent sensors and actuators. It provides a digital point-to-point connection, enabling bidirectional communication between devices and control systems. IO-Link devices transmit their data cyclically in an F-sequence (data frame), with up to 32 bytes of process data per device. The validity of the process data is signaled by the PD Valid indicator
ifm IO-Link Masters, such as the AL1350, are gateways that connect up to eight IO-Link devices to your network. They transmit machine data, process parameters, and diagnostic data to controllers and support various industrial communication protocols. These masters automatically detect connected IO-Link devices and allow communication for calibration, configuration, and data extraction.
SensorConnect is designed to connect specifically to ifm IO-Link Masters, enabling data acquisition from the connected IO-Link devices.

To interpret the process data from IO-Link devices, IO Device Description (IODD) files are required. ifm IO-Link Masters provide process data as hex-encoded strings by default. IODD files, which are XML files, contain information about the sensor’s data types, units of measurement, and parameter settings. SensorConnect automatically downloads, caches, and interprets these IODD files, converting raw sensor outputs into meaningful, human-readable JSON data.
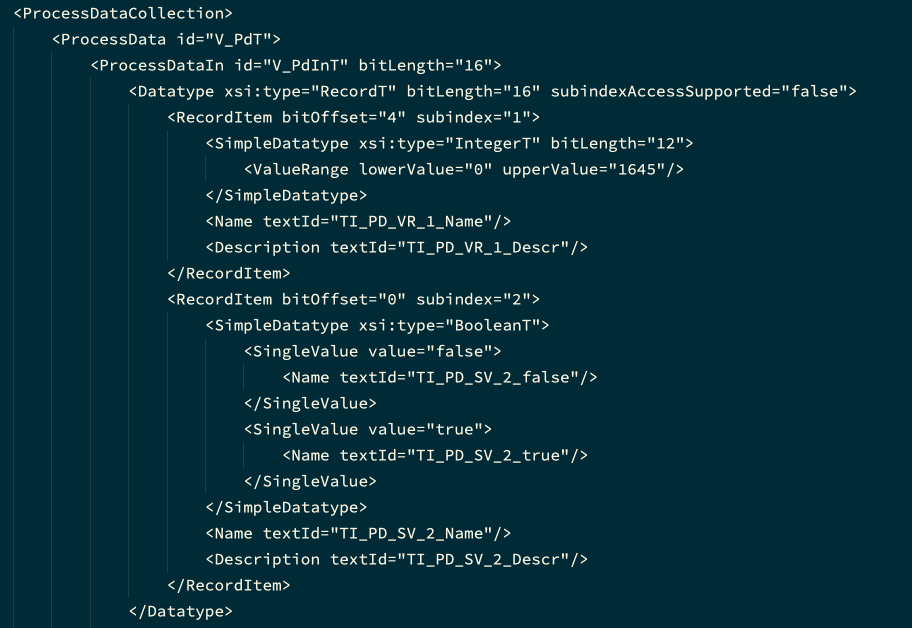
Getting Started
To start using SensorConnect with the Management Console:
- Update your UMH to the latest version using the Upgrade button in the Management Console.
- Create a New Connection and enter the IP address of the ifm IO-Link Master.
- Add a Protocol Converter, selecting “sensorconnect” as the protocol.
- Deploy and Save your configuration.
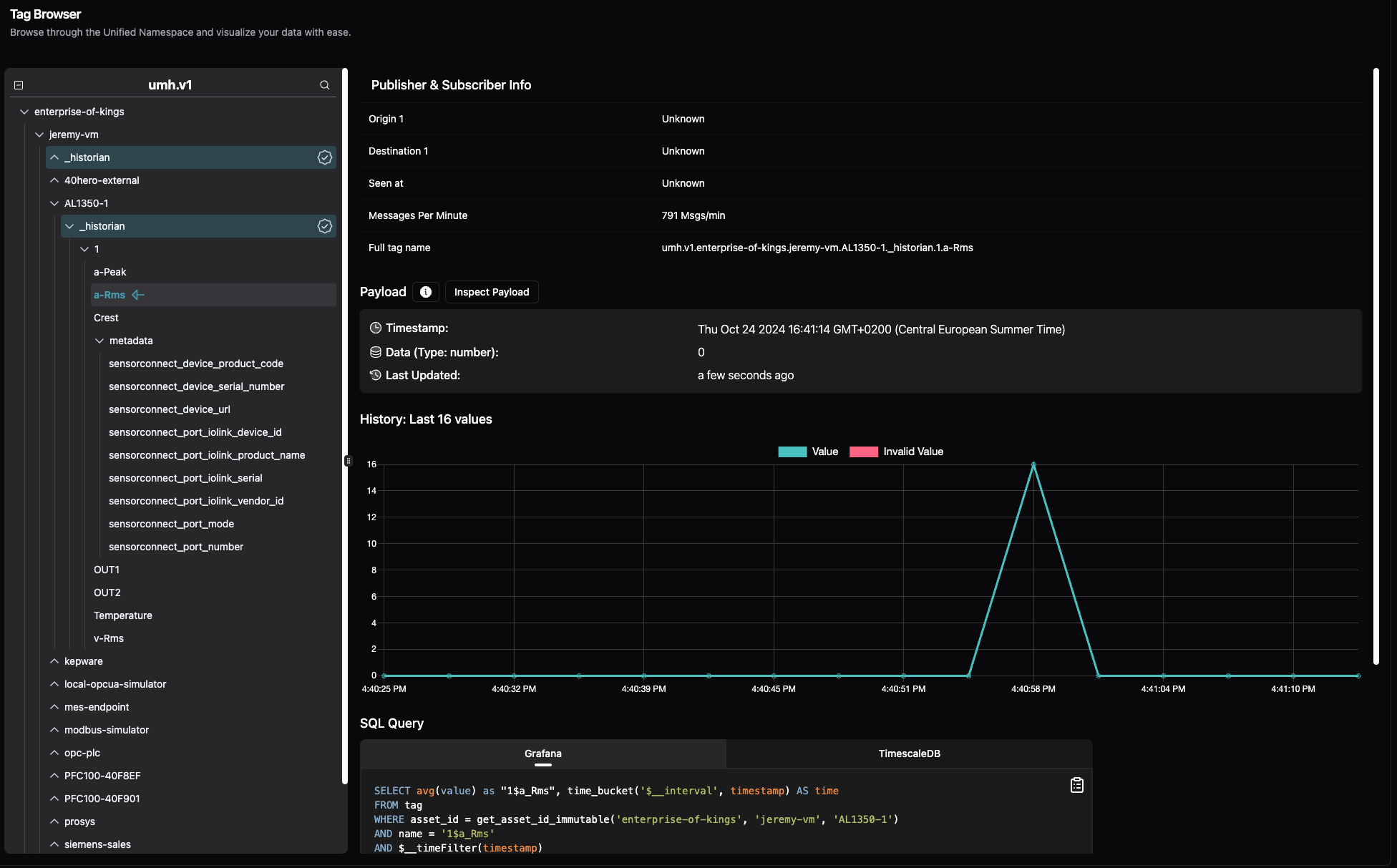
Now, you should see the sensor data in your Tag Browser.
Using SensorConnect with Benthos-UMH
The UMH Protocol Converters are based on the open-source benthos-umh, where SensorConnect acts as a new input plugin.
Below is a sample configuration:
input:
sensorconnect:
device_address: '192.168.0.1' # IP address of the IO-Link Master
If you use benthos-umh directly (without the UMH Protocol Converter), you will need to add your own processing and output configurations (such as MQTT or Kafka outputs).
Configuration Parameters
device_address
: IP address of the IO-Link Master.
Example Output
When connected to a VVB001 vibration sensor, SensorConnect outputs a JSON object:
{
"Crest": 41,
"Device status": 0,
"OUT1": true,
"OUT2": true,
"Temperature": 394,
"a-Peak": 2,
"a-Rms": 0,
"v-Rms": 0
}
Using the default processing template when selecting “sensorconnect” as a protocol converter, the data will automatically conform to the _historian data contract (e.g., it will include a timestamp and all metadata).
Conclusion
SensorConnect simplifies the process of connecting ifm IO-Link Masters to the Unified Namespace (MQTT + Kafka). Get started now ➜ https://management.umh.app