TLT Automation’s patented elliptical picker, developed with Siemens IPCs, sets a new standard for mushroom harvesting. Diederik Vermeersch, an independent system integrator, connects these mechanical breakthroughs with an open-source data stack—the United Manufacturing Hub (UMH), Benthos, Node-RED, and TimescaleDB.
This article spotlights how TLT merges mechanical innovation and real-time data flows to boost throughput, reduce bruising, and simplify operations.
By pairing cutting-edge robotics with flexible data infrastructure, TLT achieves tangible ROI while remaining adaptable to diverse farm setups.
Mushroom farming often faces high labor costs, difficult working conditions, and risks of product damage. TLT’s solution addresses these challenges by collecting extensive operational data and using advanced automation to minimize manual effort.
We’ll examine three aspects of TLT’s approach:
- A) Robust Data Infrastructure & Tools
- B) Business & Labor Impact
- C) Diederik’s Integration Role & Future Outlook
A) Robust Data Infrastructure & Tools
TLT goes beyond groundbreaking mechanics by establishing a unified, data-centric architecture.
Each machine, controlled locally by a Siemens IPC, generates up to 1,500 tags per second, capturing granular details in real time. Initially, Node-RED offered quick data-extraction and visualization, but the growing data load exposed its limitations. TLT then moved to Benthos UMH, designed for high-throughput environments, and then just used Node-RED for visualization. Benthos subscribes to entire OPC UA folder structures and applies DataOps principles to organize tags in the UMH’s Unified Namespace. This approach enables TLT to monitor a vast array of parameters in real time, making the solution highly adaptable as production scales up.
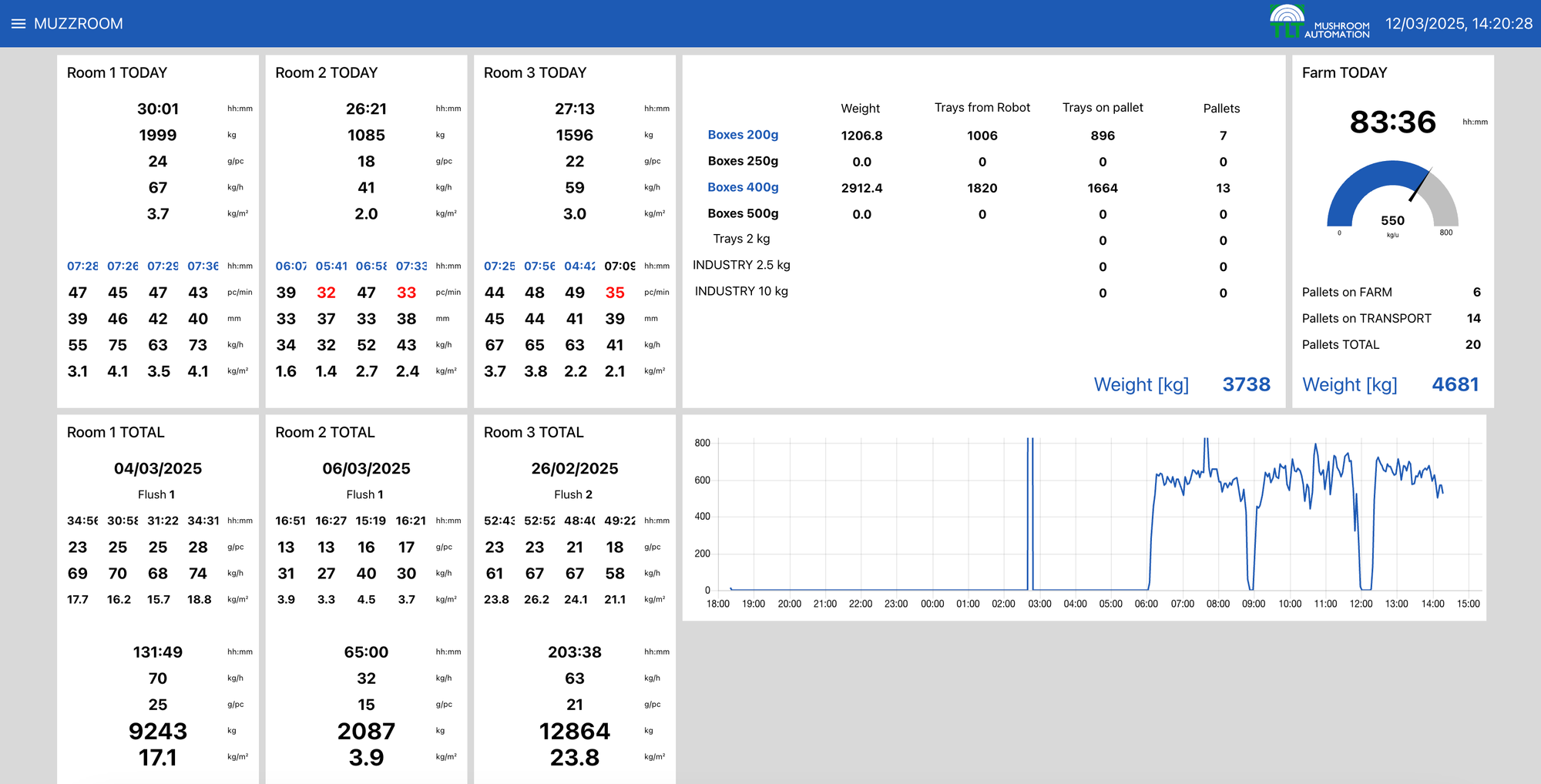
Using the UMH, TLT provides a minimal MES application that allows operators to record finished pallets using an iPad. When a pallet is marked complete, a label is printed and subsequently scanned upon arrival at the next facility, ensuring automated traceability and consistent daily and monthly production reports.
All data is stored in a TimescaleDB-backed historian, enabling real-time dashboards for throughput, machine performance, and environmental parameters. This foundation also accommodates future ML tasks—such as correlating 3D scanner outputs with environmental changes—without re-architecting the system.
Unlike traditional SCADA systems, which can be rigid and expensive to scale, TLT’s open approach uses containerized components that adapt to various farm layouts. Whether upgrading from plastic trays in Belgium to cardboard boxes in Ireland, the system remains consistent. To address cybersecurity concerns, TLT typically segregates machine networks (PLC level) from the production network using a DMZ approach, minimizing potential attack vectors. All external communications rely on outgoing MQTT connections to a central Intel NUC. That Intel NUC runs Proxmox, which hosts two virtual machines: one dedicated to the UMH stack on Ubuntu Desktop LTS, and another running essential Docker containers.
For organizations seeking guaranteed updates, bug fixes, and enterprise-grade security, the UMH Enterprise Edition is available. Though TLT and Diederik currently rely on Community Edition and internal documentation, larger organizations often prefer Enterprise licenses to ensure they’re not reliant on a single specialist for support.
By unifying mechanical design with open, containerized data infrastructure, TLT lays a scalable groundwork. The result is comprehensive process visibility, lower operational friction, and a future-ready platform for advanced analytics.
B) Business & Labor Impact
An increase in the picking rate substantially reduces labor costs, often cited as up to 50% of production expenses in mushroom farming. With real-time dashboards, operators are more engaged, competing for higher yields and responding quickly to downtime or slowdowns.
Precise handling is crucial because mushrooms bruise easily. TLT employs a 3D IFM camera to scan each mushroom’s size and color; any suboptimal picks are flagged, minimizing wasted product. This consistent scanning also extends shelf life by reducing damage, an advantage that yields higher-quality outputs and fewer returns or rejections.
Workers face less physical strain by focusing on picking alone while automated conveyors sort and pack. Real-time performance metrics foster a sense of teamwork—and sometimes friendly competition—leading to higher morale.
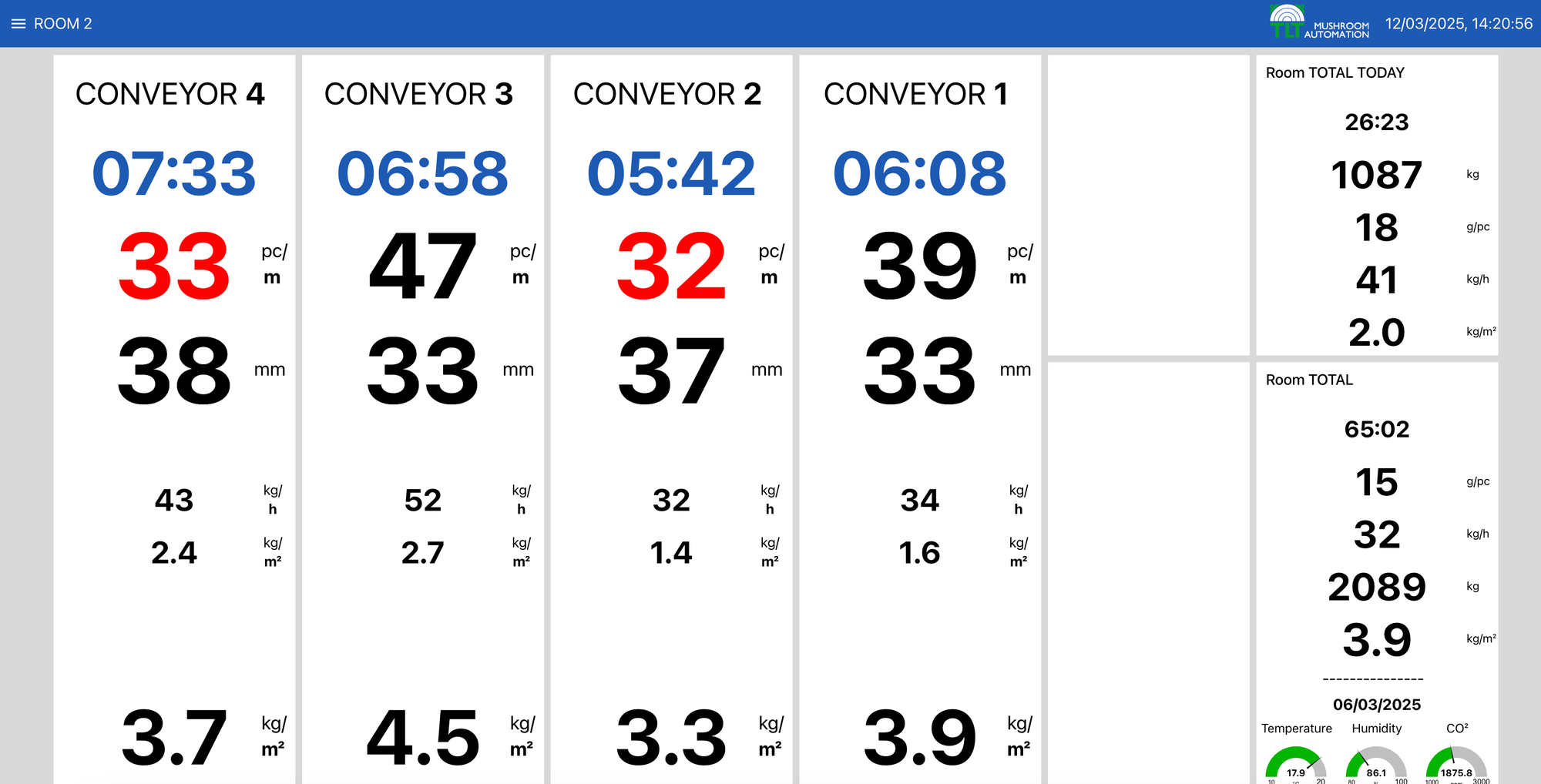
Not every farm can switch to an advanced automation stack overnight. TLT typically starts with a single line or station, using existing Siemens controls as a base. Additional components—Benthos UMH, Node-RED dashboards, TimescaleDB—are introduced step by step, minimizing downtime. This phased rollout allows farm managers to validate ROI before committing to a full-scale upgrade.
Upfront expenses include robotics and data platforms, but labor savings and better quality accelerate payback. If internal teams worry about maintenance, TLT provides documentation and training; UMH Enterprise adds an extra layer of support and security.
C) Diederik’s Integration Role & Future Outlook
Diederik’s journey with TLT began during his school years, forging early connections with the company’s founders. Later, while working on projects at Siemens, he rejoined forces with TLT to develop an innovative inverse kinematics algorithm that transforms a standard delta picker into an elliptical system. This patented design expands the picking area and enables TLT to achieve the desired throughput with fewer robots, resulting in a more cost-effective and efficient operation.
As both a system integrator and digitalization architect, Diederik has been instrumental in maximizing TLT’s impact at customers. He developed Benthos UMH flows for automated labeling, pallet tracking, and environment-based machine learning studies—establishing a digital layer that standardizes data across deployments.
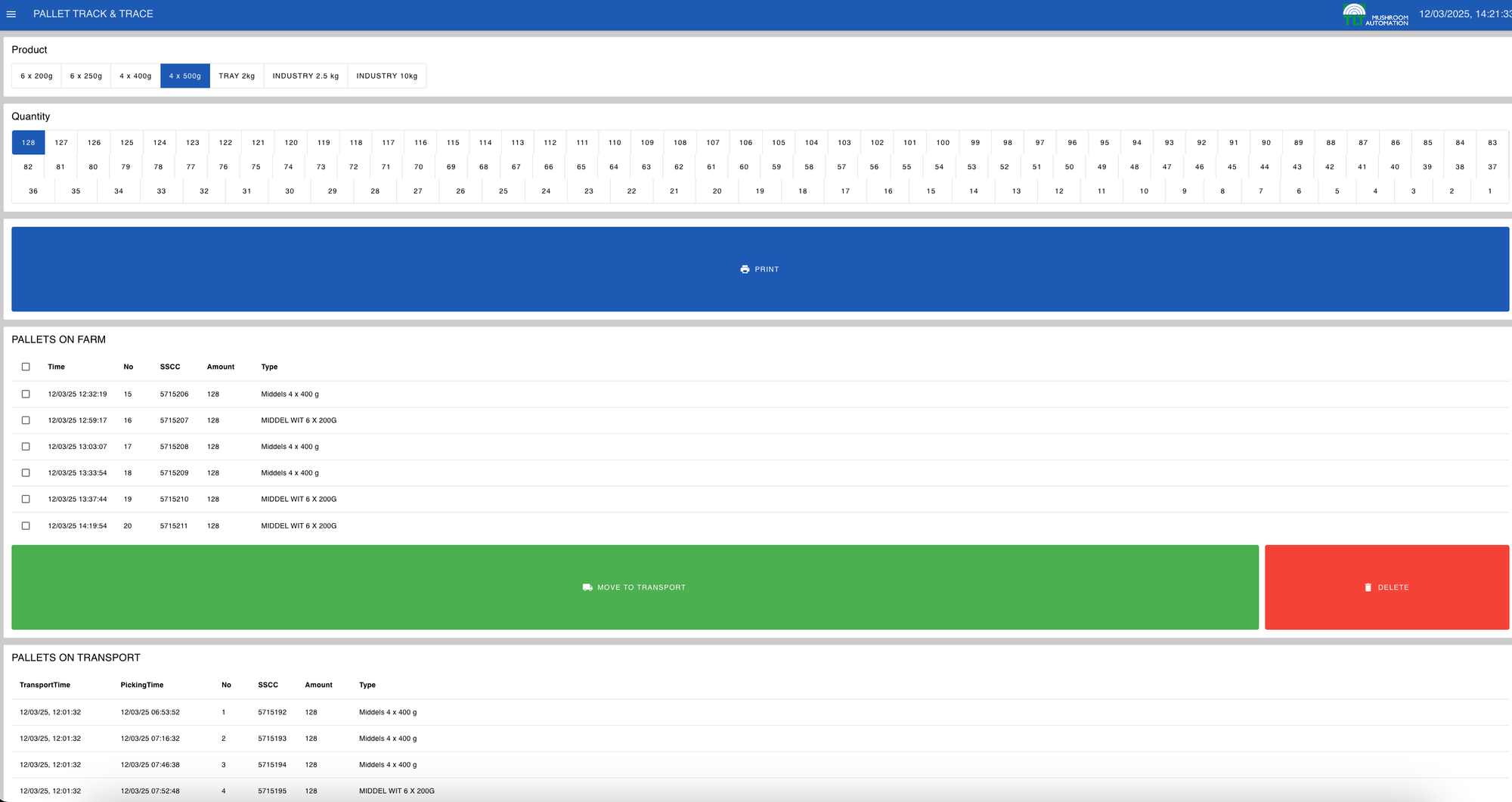
His meticulous documentation ensures that internal teams can manage daily workflows independently. Diederik’s approach enables TLT to replicate the UMH/Benthos/Node-RED stack at new sites with minimal disruption: farms start with a core Siemens PLC for the patented elliptical pickers and then layer on UMH components for real-time visibility.
As throughput data and operator metrics validate the system, TLT incrementally deploys additional lines and advanced features such as 3D scanning and environment-based ML. Looking ahead, TLT is piloting prototypes for fully robotic picking, with the same robust data pipeline supporting heavier sensor loads and more complex kinematics.
Through his commitment to open architecture and comprehensive documentation, Diederik ensures that TLT’s innovations can scale sustainably while maintaining internal expertise.
Conclusion
Who imagined delicate mushrooms could thrive under a fully data-driven approach?
TLT Automation unites Siemens IPCs, UMH, Benthos, and Node-RED to revolutionize mushroom farming. The result: higher throughput, reduced bruising, and a clear path for incremental adoption.
Interested in TLT’s setup or UMH integration?
- TLT Automation: Mechanical solutions & pilot projects
- Diederik Vermeersch: UMH deployments
By aligning patented robotics with a modern data stack, TLT paves the way for a new era in mushroom cultivation—one that boosts profits, lightens the physical burden on workers, and redefines how producers handle delicate crops at scale.