“Industrial IoT Platforms are the future of manufacturing!” This pitch echoes across boardrooms, trade shows, and vendor demos, promising a single, all-encompassing solution to every IT/OT challenge. Yet, in our experience, the reality is more nuanced. Enter the Unified Namespace (UNS)—a concept that claims to unify and organize manufacturing data at scale. Which approach wins out, and why?
My team and I have spent years working on industrial digitalization projects. We launched a system integration venture back when “UNS” was still in its infancy. At the time, the big promise was the Industrial IoT Platform, touted as “the missing piece” to finally connect OT (Operational Technology) and IT. Sound familiar? In many ways, it parallels today’s UNS pitch.
In this article, I’ll combine real-world observations with some technical fundamentals to offer our perspective on Industrial IoT Platforms, the UNS, and how to choose—or combine—these approaches effectively.
We’ll break this down into three core parts:
- The Reality of Industrial IoT Platforms — strengths, weaknesses, and real-world pitfalls.
- What the UNS Brings to the Table — how it addresses common IoT platform shortcomings.
- Striking a Balanced Approach — combining both IoT platforms and the UNS for a win-win.
1. The Reality of Industrial IoT Platforms
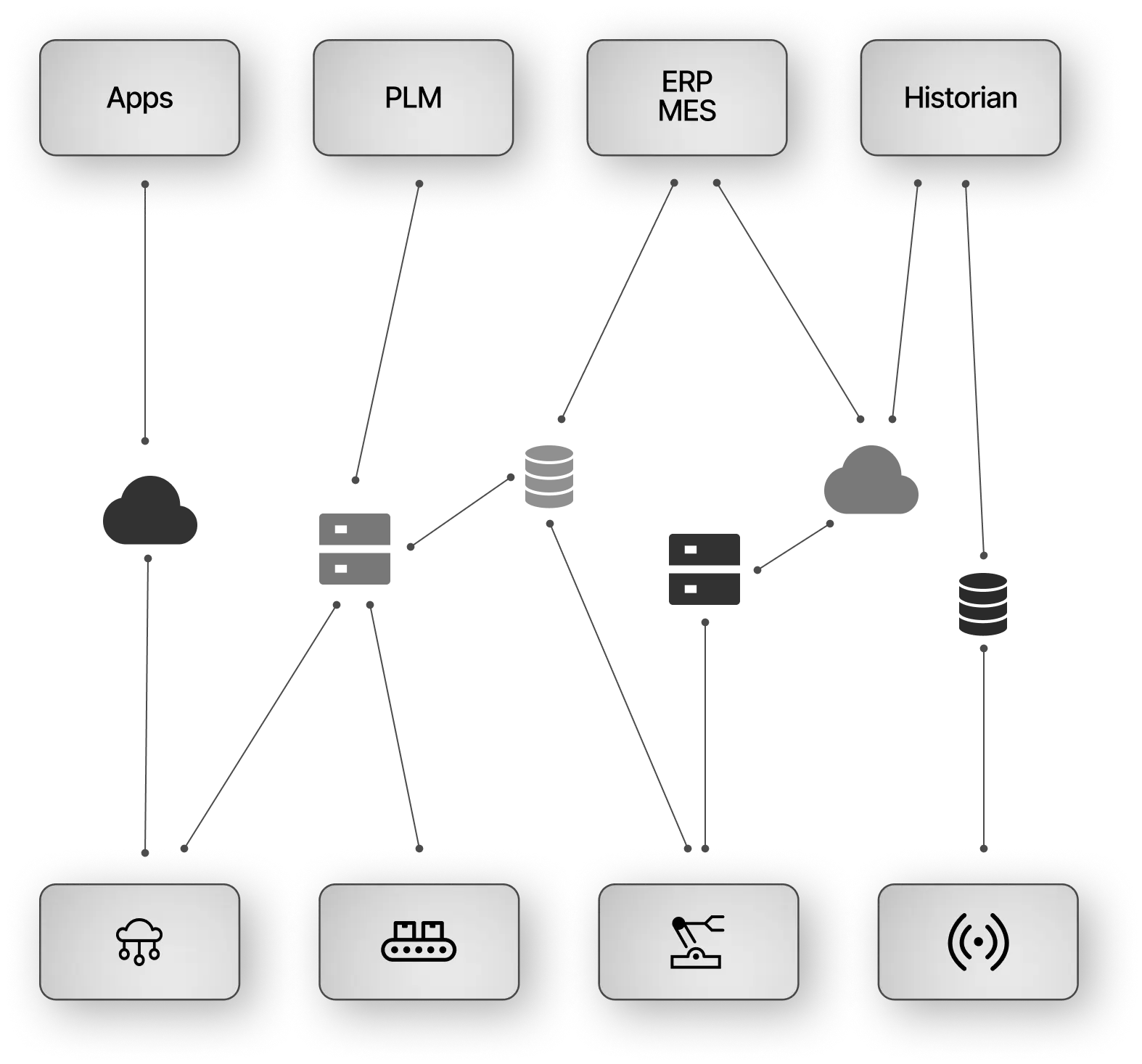
Industrial IoT Platforms promise rapid development of applications with minimal technical overhead—yet they often underdeliver due to data and scalability issues. The pitch often goes something like this:
“To stay competitive, you need digital technologies to optimize OEE, first-pass yield, maintenance cycles, etc. But you lack on-site skills, so our IoT platform lets you build solutions quickly and cost-effectively.”
Lack of a Universal Definition:
IoT platforms aren’t universally or axiomatically defined. In the simplest terms, an Industrial IoT Platform is a single software solution—either on-premises or cloud-based—that aggregates industrial data for faster, low-code application development.
Major Vendors:
Examples include ThingWorx, Cumulocity IoT, MindSphere, and Predix, each aiming to speed up digital transformation with minimal coding.
Where It Falls Short
Data Quality & Quantity:
Many organizations don’t have robust, high-quality data pipelines in place. Because IoT platforms typically sit at the “end of the pipeline,” they don’t inherently solve data connectivity or aggregation challenges. Without good data, even the best platform can’t deliver meaningful applications.
Unidirectional Flow:
Traditional IoT platforms often focus on pulling data out of the shop floor and into dashboards or analytics, but rarely facilitate sending real-time data back into operational systems—limiting their ability to replace or augment traditional SCADA or MES use cases.
Scalability Limitations:
Handling a few data points is easy—pushing temperature readings into an API and toggling a rule on change, for instance. But ingesting thousands of data points per second can bog down most IoT platforms, causing performance bottlenecks.
Illustrative Scenario:
- Build Your Apps
- You invest heavily in creating applications within the IoT platform.
- "onChange Triggers" Multiply
- Numerous scripts for data transformations evolve into spaghetti logic.
- System Performance Degrades
- Real-time responsiveness plummets as data volume soars.
- Data Aggregation
- Management or vendors question the need for granular real-time data, prompting aggregation and a loss of detail.
- Integration Challenges
- New apps or vendors require richer, more detailed data and bypass the IoT platform altogether—connecting directly to plant-floor systems like Kepware.
Vendor Lock-In & Ecosystem Limits:
Many IoT platforms push for an all-in-one ecosystem, making it difficult to integrate best-of-breed tools. This forces you to develop all your use cases inside a single platform, preventing you from leveraging specialized solutions (e.g., OEE, MES, CMS, or QMS) that could offer better speed and quality for particular tasks.
A single, monolithic IoT platform can work for certain scenarios but often struggles under industrial-scale data demands. Let’s see how a Unified Namespace aims to tackle these scalability and integration challenges.
2. What the UNS Brings to the Table
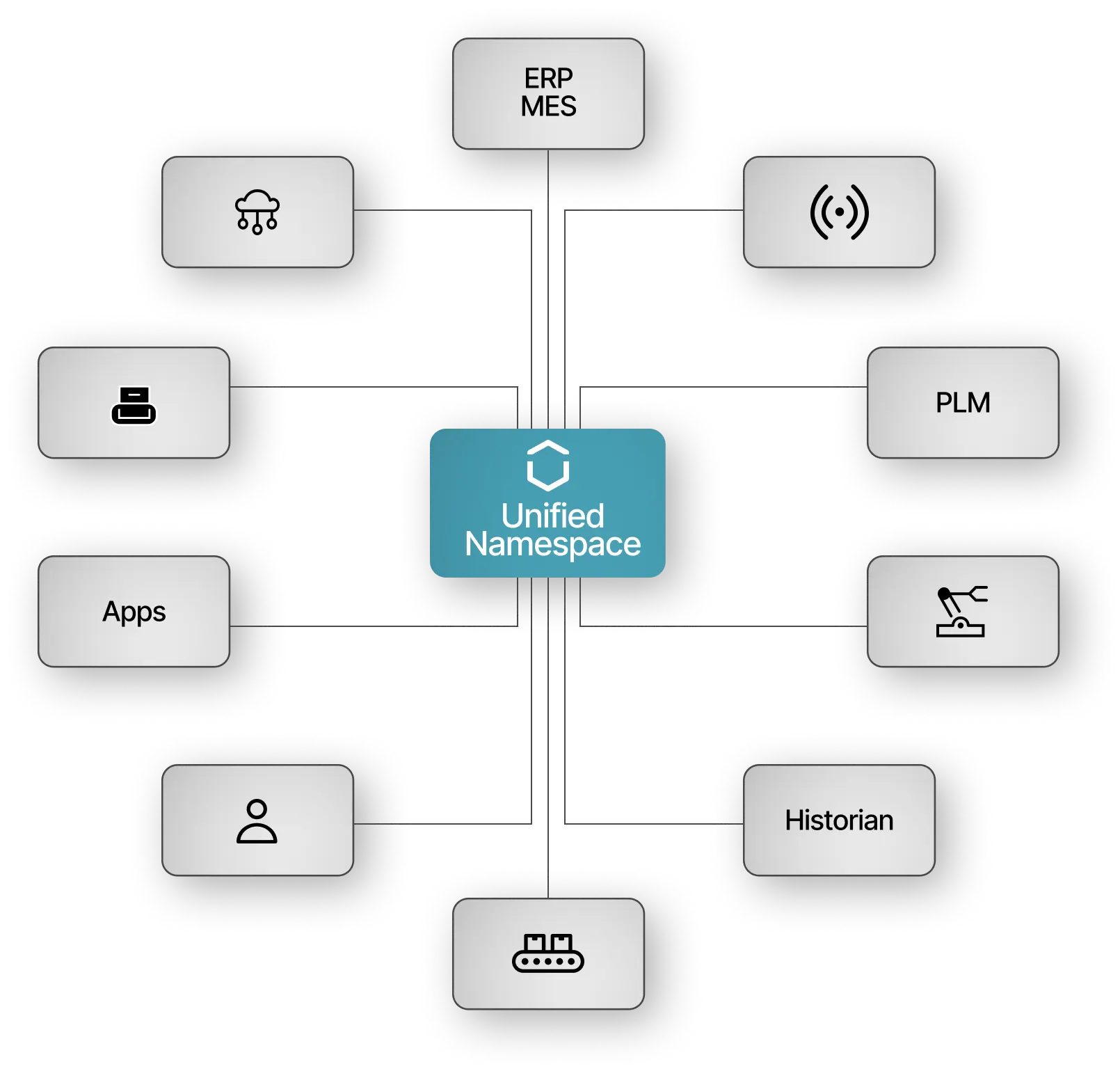
A Unified Namespace is an event-driven data architecture designed to serve as the single source of truth for all manufacturing data. A typical sales pitch might sound like:
“With the UNS, you create a scalable data foundation that makes all data available in one place. This reduces time to value for new use cases and removes technical limits that could hinder your scalability.”
Core Concept
The UNS extends the classical ISA-95 hierarchy, providing a structured, API-first approach (commonly via MQTT or Kafka) for real-time and asynchronous data exchange.
Reduced Time-to-Value
Once the UNS is established, each new project doesn’t have to recreate the entire data-gathering and contextualization process.
How It Works
- Event-Driven:
- Subsystems publish updates to the UNS in real time (e.g., sensor data, machine states). Consumers subscribe as needed, without complicated point-to-point integrations.
- Open for Everyone:
- The UNS doesn’t restrict who produces or consumes data. It’s a foundational layer that any application—analytics tool, IoT platform, ERP system—can connect to, so long as they speak the right protocol.
Where It Falls Short
Lacks Native Historical Context
The UNS often provides only current values or real-time snapshots. A separate time-series or relational database is needed for historical queries.
No End-to-End Use Case
The UNS by itself isn’t turnkey. It enables other apps and integrations for analytics, dashboards, or advanced automation but doesn’t provide them natively.
If Industrial IoT Platforms suffer from siloed complexity while the UNS excels at flexible data distribution, how do we strike a balance that captures the best of both worlds?
3. Striking a Balanced Approach
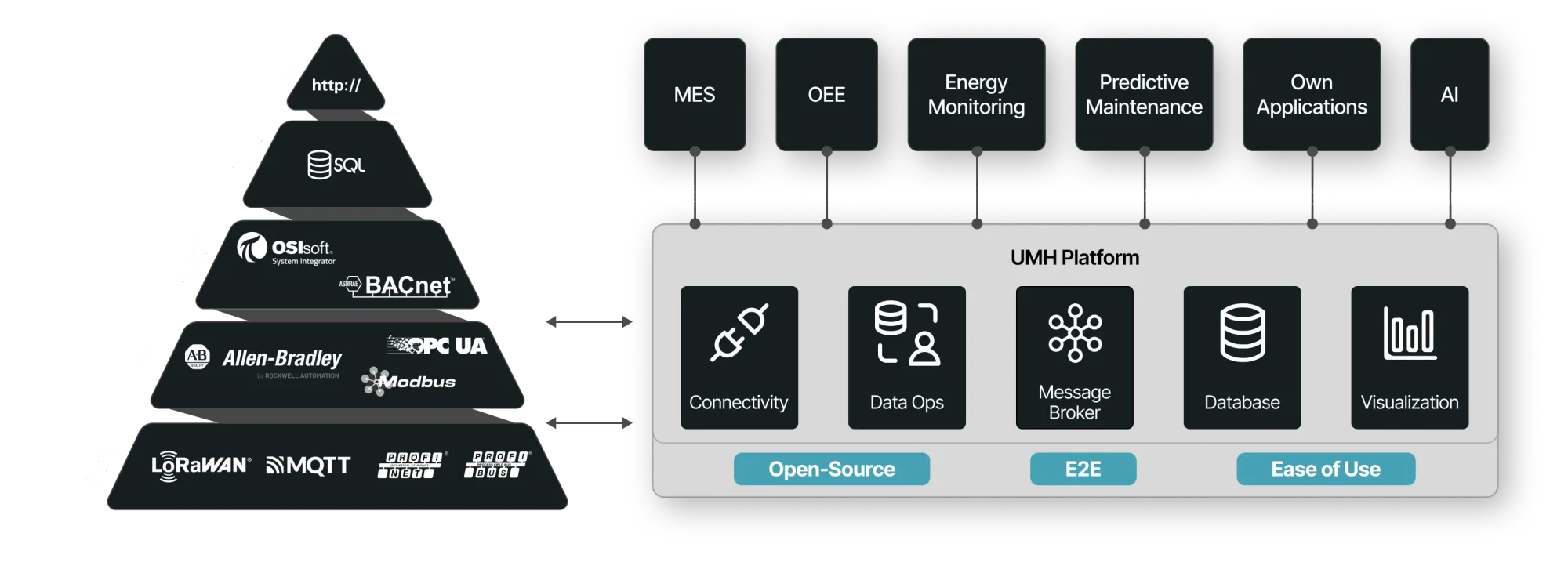
To get the most out of both, use a UNS for flexible, high-quality data exchange and treat IoT platforms as specialized applications rather than monolithic, one-stop shops.
Queryable UNS
Automatically store real-time data in a database (e.g., PostgreSQL + TimescaleDB) that mirrors the UNS structure. This allows for quick lookups, time-series queries, and analytics.
IoT Platforms as “Apps”
Avoid vendor lock-in by ensuring your IoT platform supports standard APIs (MQTT, Kafka, REST) to read and write data. This way, if you change platforms or add specialized solutions later, your data layer remains intact.
Prove Value Quickly
Deploy your UNS alongside a specific, value-adding application—like an OEE dashboard or an energy optimization module—to demonstrate ROI and secure stakeholder buy-in.
Example
- Data Publication
- Machine data (PLCs, sensors, SCADA) is published in real time to the UNS.
- Data Persistence
- A bridge persists these events in a TimescaleDB-based historian for historical and real-time analysis.
- Application Layer
- Specialized applications—whether an out-of-the-box IoT platform or a custom analytics tool—consume data from the UNS, apply domain-specific logic, and can even write results back. This leverages the low-code benefits of IoT platforms without locking you into one system
Wrap-Up
IoT Platforms excel at rapid, low-code application development—up to the point where you need massive data throughput or specialized integrations.
UNS excels at centralizing and distributing real-time data but doesn’t inherently provide analytics, historical storage, or end-to-end solution building.
Balanced Approach - Use the UNS for data exchange; layer IoT platforms and other specialized tools on top, ensuring everything integrates seamlessly instead of forming isolated silos.
Don’t let your critical manufacturing data get trapped in rigid, proprietary silos. By adopting a UNS as your foundation, you open the door to a broader ecosystem of best-of-breed applications—each designed for specific business needs.
If you’re intrigued by the power of a Unified Namespace and want to see this approach in action, explore our open-source IT/OT integration platform at [UMH]. We’d love your feedback—your insights help us refine our tools and push the boundaries of what’s possible in modern manufacturing.
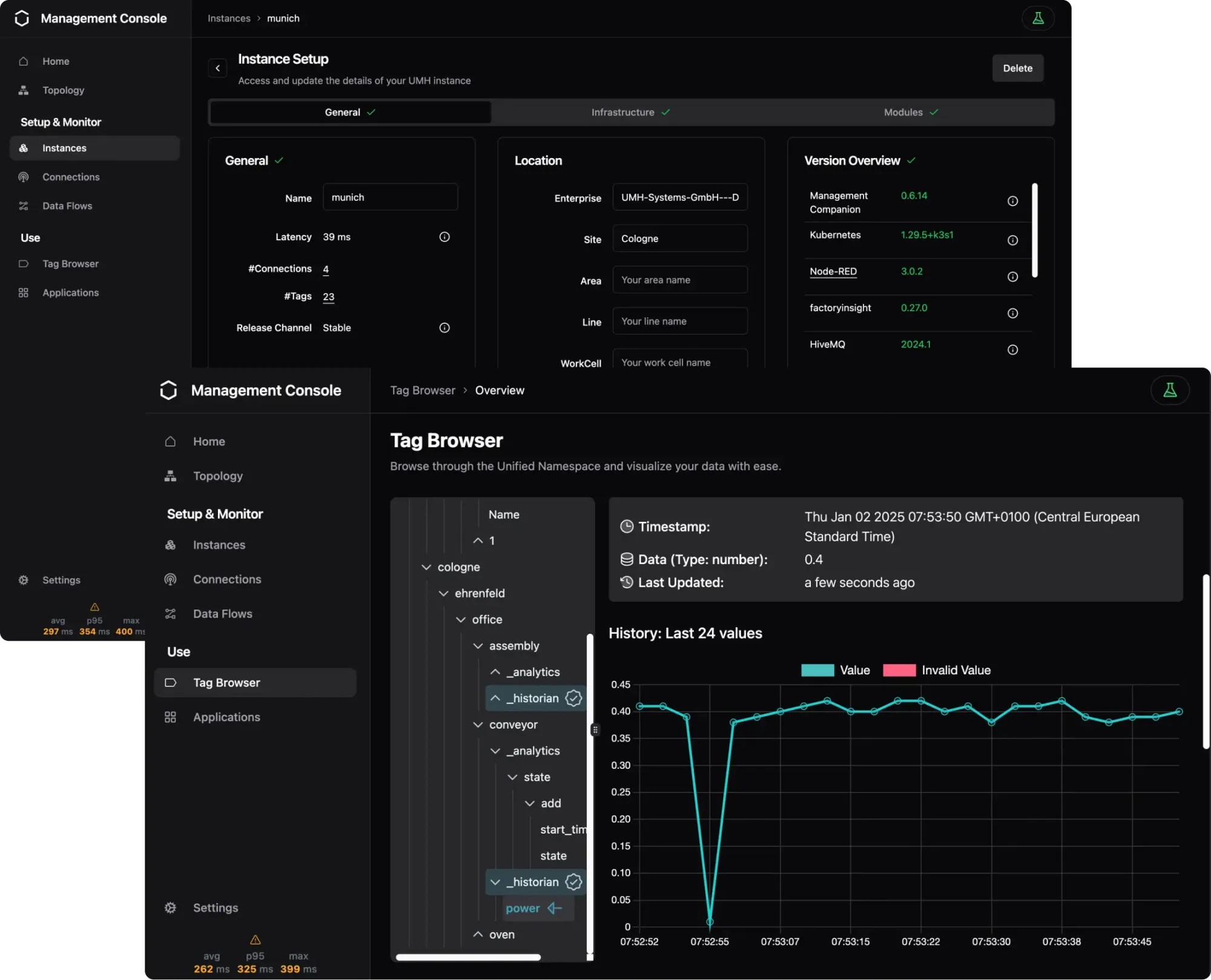
IT / OT Integration Platform for Industrial DataOps
Connect all your machines and systems with our Open-Source IT/OT Integration Platform to make all shop-floor data accessible at a single point.