In the manufacturing industry today, there is a lot of talk about Industry 4.0 and the advantages of it. Our previous blogpost – Why Industry 4.0 is crucial today – goes into this more in detail. In this article, we take a look at why some companies still struggle with digitization despite the clear advantages it brings.
The awareness of Industry 4.0 and the advantages that it brings has improved over the years. In a study done by BDO in 2019 (pre-COVID) in the UK, 46% of manufacturing firms said that they had a high understanding of digital transformation. In 2016, only 9% of firms claimed to have a high understanding.
Due to COVID, manufacturing companies’perception of Industry 4.0 has altered. A McKinsey study conducted 6 months into the pandemic showed that 65% of respondents considered Industry 4.0 more valuable. 94% claimed that Industry 4.0 had helped them stay in operation during the crisis. 56% of them stated that these technologies had been a vital part of their pandemic responses.
Despite the growing positive outlook on Industry 4.0 companies still face barriers with digital transformation. These are some of the challenges that firms face:
- Skills and Talent: One of the biggest challenges are the skills and the talent required to manage and maintain the structures of Industry 4.0. For example, with data analytics current employees might not have the skill to collect, analyze, interpret and utilize the data. In a report by PWC, 81% of the respondents expected to have difficulties in hiring talent for their digitized factories. 83% believe that they will need apprentices in areas for which there is currently no formal training. Companies are tackling this problem by creating their own development programs to upskill and train employees. However, this opportunity requires an investment that many smaller companies are not able to afford.
- Cyber Security: The second major challenge is cyber security. Due to the interconnected nature of operations in Industry 4.0, a cyber-attack would have a greater effect on a company than before. Manufacturing firms are often not prepared for this risk. Every connected device is a potential risk for a cyber-attack. Since previously isolated devices would now be interconnected to a larger system, this increases the entry points for an attacker. In order for a cyber threat to be negated, cyber security needs to be fully integrated into all the organizational and information technology from the beginning.
- High investment requirements: SME’s (Small and Medium Enterprises) often find it difficult to raise the capital that is required for the implementation of Industry 4.0. In order to reap the full benefits from Industry 4.0, it cannot be executed in an isolated manner. The entire factory needs to be integrated, and this is a significant cost. Furthermore, in addition to the investment for the digitization of the factory, existing employees will need to be trained or new employees will need to be recruited in order to effectively manage the factory.
- Organizational resistance to changes: There are clear advantages to digitizing your factory, assuming it is implemented correctly. However, despite the growing awareness of the advantages, there is still some resistance among employees in organizations to adopt these newer technologies. Often employees do not understand the full value behind adopting technologies. The technologies could improve things from a larger organizational perspective (with planning, efficiency, decision-making etc.) but might not have a direct impact on employees who operate the machines.
- Lack of infrastructure: Often companies do not have the IT and data infrastructure that is needed to successfully implement Industry 4.0 strategies. This problem is especially prominent in developing countries. Fast and secure data connection is a primary and relevant condition in order for Industry 4.0 to be successful.
Given the reasons above, it is understandable why there is still a hesitation in the manufacturing industry. However, it is imperative that companies explore the potential of digital factories. Referring to the McKinsey study, 56% of the respondents who had not implemented Industry 4.0 technologies before COVID found it hard to respond to the pandemic due to their lack of digital technologies.
Companies will also benefit greatly from a cost standpoint in the long run if Industry 4.0 is implemented correctly. With the technology, companies have been proven to have lower operating costs and improved product qualities. A study by Mckinsey on the potential of Industry 4.0 shows that it can reduce the operational downtime of a machine by 30-50% and improve the quality of the product by 10-20%. This would increase a company's competitive advantage in the market.
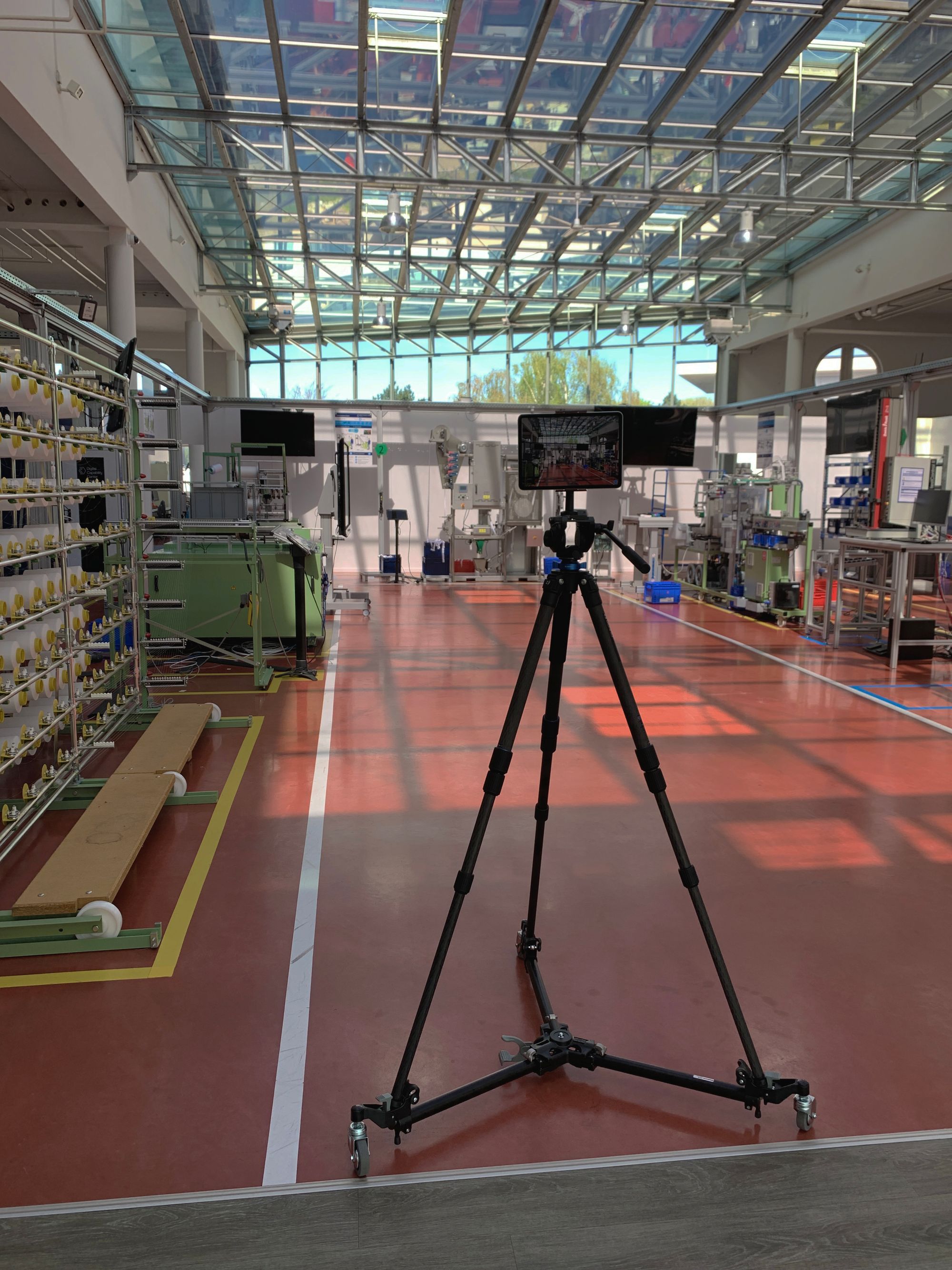
Industry 4.0 would also give firms flexibility to react to changes in the production line. This ability to react quickly in the market during unpredictable occurrences like COVID or a change in demand is invaluable and companies can benefit greatly from it.
There are many more advantages that Industry 4.0 can bring to your company (increased customer satisfaction, easier compliance, better documentation and communication etc.). Therefore, despite the potential barriers that companies will face, it is imperative that they start the process toward digitization before they lose any competitive advantage.
If you want to learn more about IT and OT, you can read more about them on our learn page. In order for Industry 4.0 to be successful the two worlds of IT and OT need to be merged. You can read more about that in our blog article here.