More and more manufacturers are offering their software platforms everywhere on the internet as a panacea for simplifying and optimizing all production processes. But can this really work?
Despite the increasing convergence of IT and OT, companies should think twice before using one system to handle both areas. This is because, historically, the vast majority of providers have their roots in either IT or OT.
How did this happen, and why does the history of IT and OT make it advisable to separate the two?
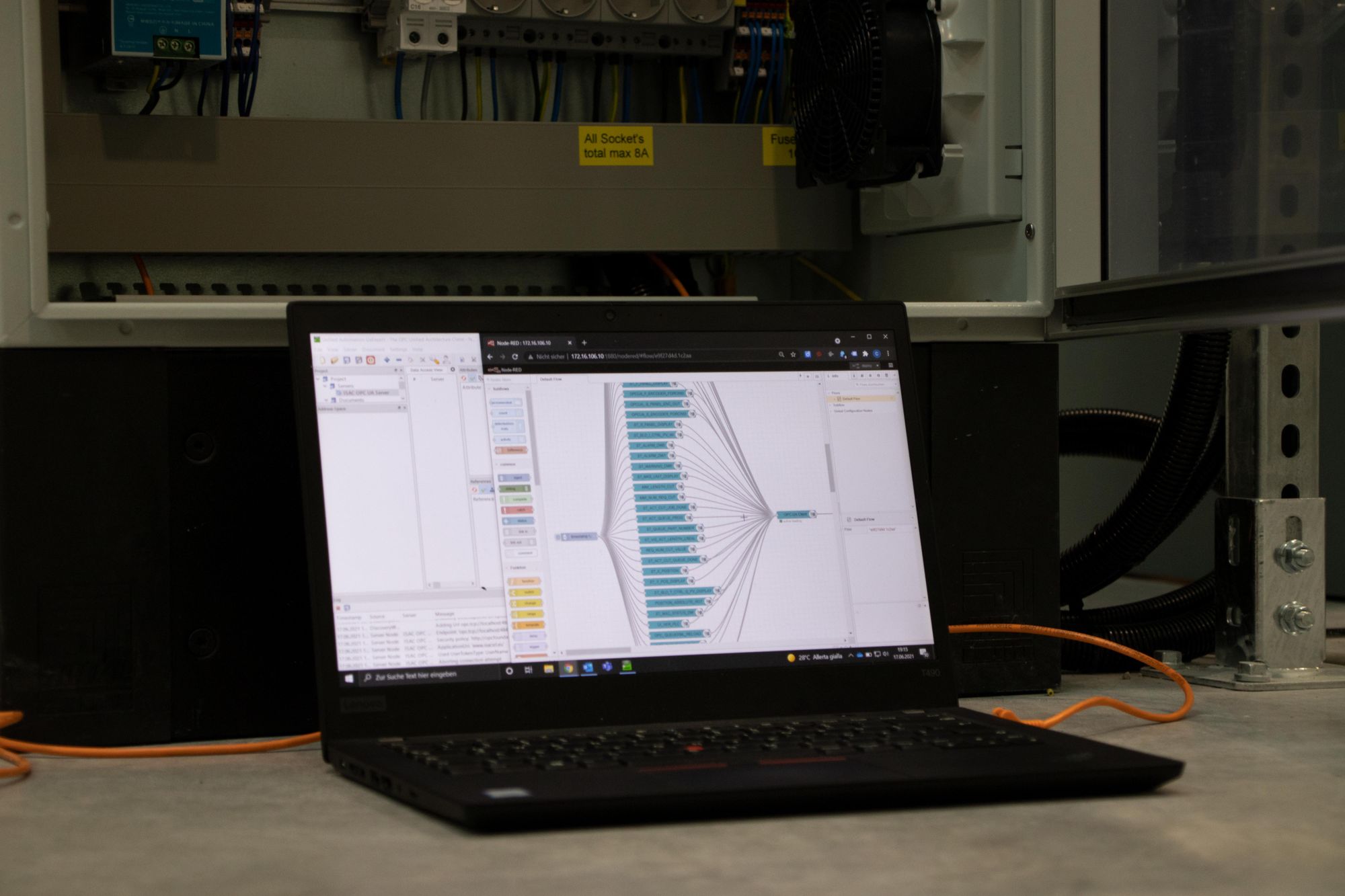
In this picture, IT and OT are combined using UaExpert and Node-RED together with industrial equipment, e.g., industrial edge computer from OnLogic, network switch from WAGO and an electrical rack, to extract and process data in manufacturing.
The beginnings
After the first two major shifts in the world of work were spurred by the steam engine in the 1800s and the assembly line in the early 20th century, the introduction of microchips in the 1970s started the Third Industrial Revolution. Due to the shift from mechanical and analogue electronic technology to digital electronics such as digital computers and record-keeping it is also known as the Digital Revolution.
Personal computers made their way into offices and private households, forming a new branch of industry. Programmable logic controllers (PLCs) and computer numerical control (CNC) machines also drove this revolution.
From then on, further development was divided into two major areas: Informational Technology (IT) and Operational Technology (OT) or automation.
The long road to Industry 4.0
What began in IT with simple .exe files quickly developed into increasingly complex software systems. Even then, the first programming languages were SQL, Prolog or C++, which still form the basis for a wide variety of software today.
With the introduction of more and more new operating systems like MS-DOS (1981) or revolutionary new applications like Office (1989) new possibilities arose. From the mid-1990s onwards, it was possible to access the Internet via the telephone line at a maximum speed of 56 kbit/s. Increasingly larger quantities of data were created, leading first to floppy disks, later to CD-ROMs, and USB sticks.
Today, we usually store data cloud-based (One-Drive, Google Drive, Dropbox etc.). Modern software applications such as machine learning and predictive analytics, Kubernetes and Docker now enable us to do things that were undreamed of back in the beginnings.
Similar to IT development, automation has also evolved.
The first PCs were used from the 80s as a direct interface to PLCs. Together with software improvements, this made monitoring machine processes much easier. In the '90s, more and more user requests led to programmable human-machine interfaces (HMIs) that could clearly display errors to users, for example.
Machine monitoring information became increasingly important, leading to a new generation of PLCs and thus internet connectivity on factory floors in the late 1990s. Digital networking made it possible to coordinate machines, save time and resources, and produce individual requests economically, even in small quantities.
Digitalization has made it inevitable that the two - keyword: IT and OT convergence - will converge again!
The Internet of Things
We know this convergence as the IoT ("Internet of Things"), which is a network of devices that communicate with each other and provide data to users over the Internet.
A subcategory of this is the IIoT, the Industrial Internet of Things.
The term refers to IT technologies used in the industrial environment (especially in manufacturing facilities), thus leading to the convergence of IT and OT. The IIoT represents communication between the machine networks and provides plant managers with data that gives a clearer picture of how equipment is operating.
With the data collected, they can increase efficiency, productivity, but also employee safety. However, this brings together different disciplines.
Because of the history of IT and OT, companies usually have either an IT or OT focused background and therefore are only experts in their specific field. This leads to challenges when it comes to merging the two areas.
Challenges for IT and automation
In the IT-world companies too often focus on building up generic IoT platforms and programmable dashboards but lack experience with the classic production environment.
As a result, companies with an IT specialized background are able to create nice looking and well working IT solutions but often use non-industry ready hardware to bridge the gap to the OT-world.
As an example, Raspberry Pis (a single board computer) is used in a production environment instead of Revolution Pis, which are specifically designed for industrial use. The difficulties this has for reliability are well known.
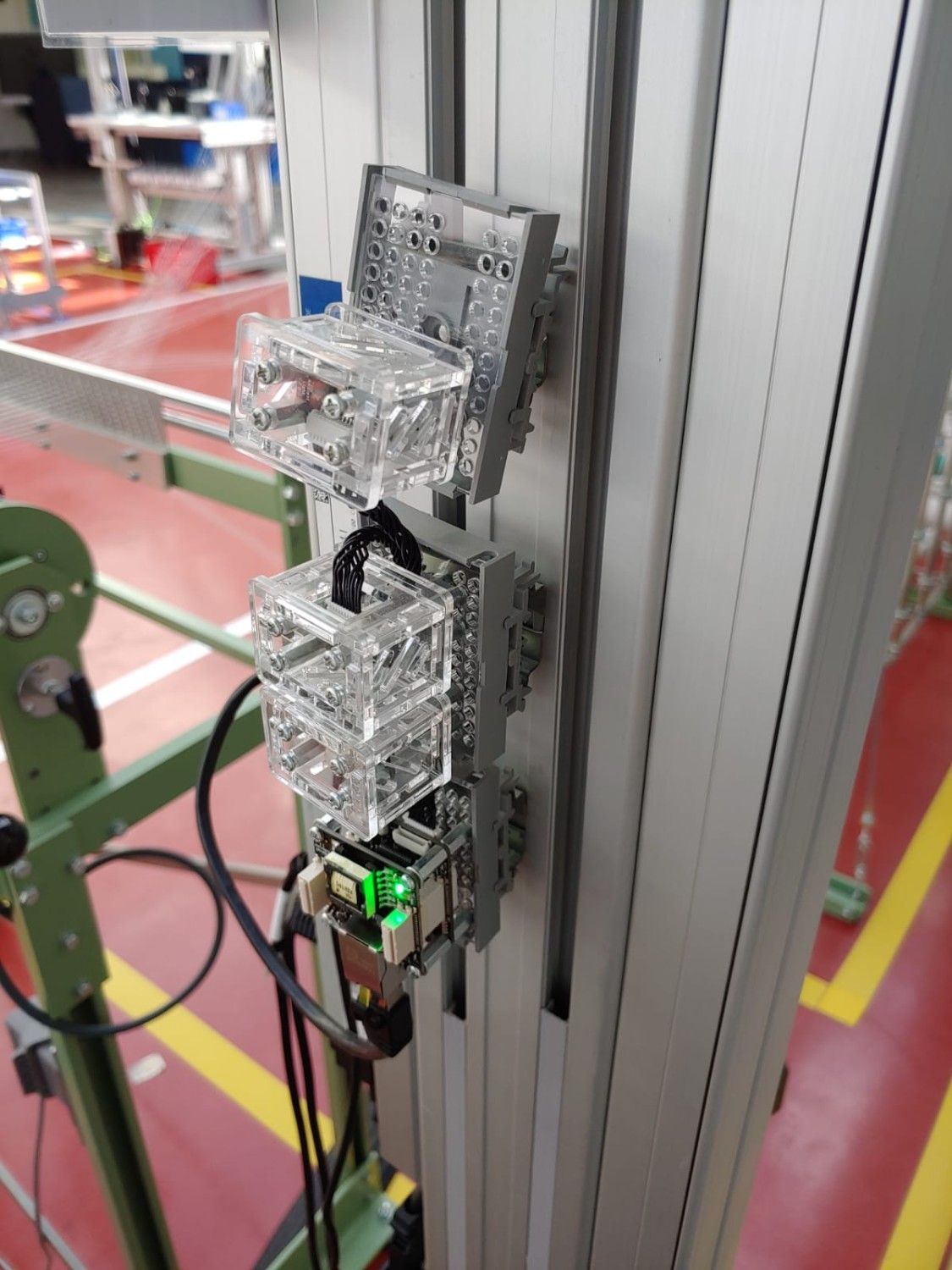
Another challenge is that defined interfaces do not fit the heterogeneous production landscapes. Those interfaces sound good in theory, but anyone who has stood in front of a 30-year-old machine (or a sealed off machine under warranty) knows that simply connecting is often next to impossible.
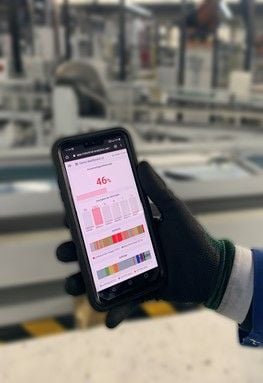
In the OT-world on the other hand, many companies in the automation industry use PLCs or certified hardware but don't have many options when it comes to IT-applications.
Lack of know-how regarding standards as well as bad experiences lead to wrong choices by deploying IT solutions. But as long as the application is stable, concerns such as usability or ergonomics tend to be neglected.
The same applies to scalability or flexibility. Yet those are precisely the features that are crucial for modern production environments.
In practice, missing knowledge (of VLANs or subnets, for example) leads to the development of messy applications where more and more elements and features are added later. This results in systems that are highly complex which limits future growth.
Dashboards, analytics and reporting as well as the connectivity to the cloud and third-party systems should remain in the IT world.
So, what is the right approach to combine both disciplines?
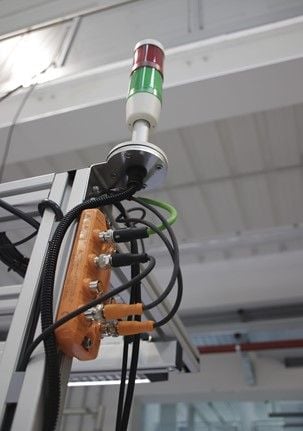
Why not using the best from both worlds?
The increasing convergence of IT and OT means that the two areas will merge more and more which is critical to meet future demands of customers.
The reason behind is that the usage of IoT and IIoT is essential to avoid falling behind competitors. Therefore, both IT and OT will be deployed in future industry solutions.
However it is advisable to always use both an IT and OT solution and connect them via an interface.
Iterative and agile methods are prooved to function well in the field of software development focused on usability but in the field of automation reliability, robustness and maintainability of the applications are the most important factors to ensure a smooth production.
By using a combination of an IT and OT solution, the user has the benefit of two systems that are specialized on their specific tasks.
The communication between those two systems takes place via an interface which adds an additional layer of security to protect the production environment and machines.
One of the respondents in the upcoming master thesis from Nicolas Altenhofen at the Institute for Technology and Innovation Management at the RWTH Aachen confirms this understanding between IT and OT:
We build some software up and it is running and I am actually totally happy. And then my colleagues come by and say "it is crashed again", and I say "yes hello, 99% availability". Then they say "yes, but not 100!".
For an IT specialist, that's actually nonsense. […] The fact that you have to increase the speed of change to remain competitive in the future and that you then have to accept that some things are not 100% fully developed is something that mechanical engineering still has to learn from my point of view.
The quote is highlighting the point that mechanical engineers build a system that needs to work 100% (i. e. nuclear reactors) while IT developers need to focus on speed and flexibility.
Conclusion
We suggest to take the best automation software on the market and let it control the operational processes according to your ideas.
The resulting data should be sent via industry standards such as MQTT or OPC/UA to what you consider to be the best IT product. (take a look at our documentation to see how the United Manufacturing Hub is connecting a MQTT-broker with OPC/UA)
When it comes to analyzing data, IT software still offers the best options. We strongly advise against automated control of production plants from the cloud, both now and in the near future.