This chapter starts by giving some background information on when and why this standard was created. Afterwards it goes into detail of what the automation pyramid is, and what the characteristics of each layer are. The chapter 2.2 Process Controls goes into detail on the first two layers. Chapter 2.3 Operations Management (MES, ERP, PLM) then explains the other three layers.
Background
During the 1990s, the adoption of PCs and networking by large enterprises became more prevalent, leading to the need for standardization of terminology between business and production processes. In 1995, the ANSI/ISA-88 standard was created to address this need, particularly in industries with batch production processes. This standard defined organizational and process definitions for the batch production industry, but it did not cover other types of industries or provide a comprehensive organizational perspective. As a result, the International Society of Automation (ISA) in the United States created the ISA-95, also known as the automation pyramid, to define a model of a company that covers all industries and includes the exchange of data between administrative and production functions. The IEC later released a corresponding standard called IEC62264-1.
In a nutshell, ISA88 introduced and defined the following concepts, separated by two types:
- Organizational: enterprise, site, area, process cell, equipment module and control module
- Process definitions: stage, operation, phase, recipe, formula, status
This standard was very well accepted by the industry, because it facilitated communication between different companies within their value chain (with suppliers and customers), but also between production sites (factories) and headquarters in the same industry. The problem was that it was covering only the batch production industry (instead of discrete or continuous processes). Also, its zoom-in approach particularly covered the production process, rather than the entire organizational perspective.
Therefore, the necessity for a new standard covering all type of industries triggered a search for a new standard, paying particular attention to the gap between production and business.
Concept
The International Society of Automation (ISA) from the United States created the ISA-95, Enterprise-Control System Integration (and later the IEC62264-1), commonly known as the automation pyramid. The objective of this standard is to define a model of a company which distinguishes the software systems used for administrative functions, production functions, and the data exchanged. In this analysis of information flow, it is also intended to assign common terminology to the types of software systems used by organizations.
Moreover, the standard is not only focused on the automation pyramid, but also provides a detailed framework for modeling the production line. This is particularly evident in layer 3, where MES and historian contextualize the data.
Lastly, ISA95 highlights the communication protocols used between the layers. From level 0 to 2, safety is crucial, therefore a local industrial network is used with fieldbus communication protocols. Layers 3 and 4 use internet-based communication protocols. The higher you move up the pyramid, the more classic IT characteristics you will find.
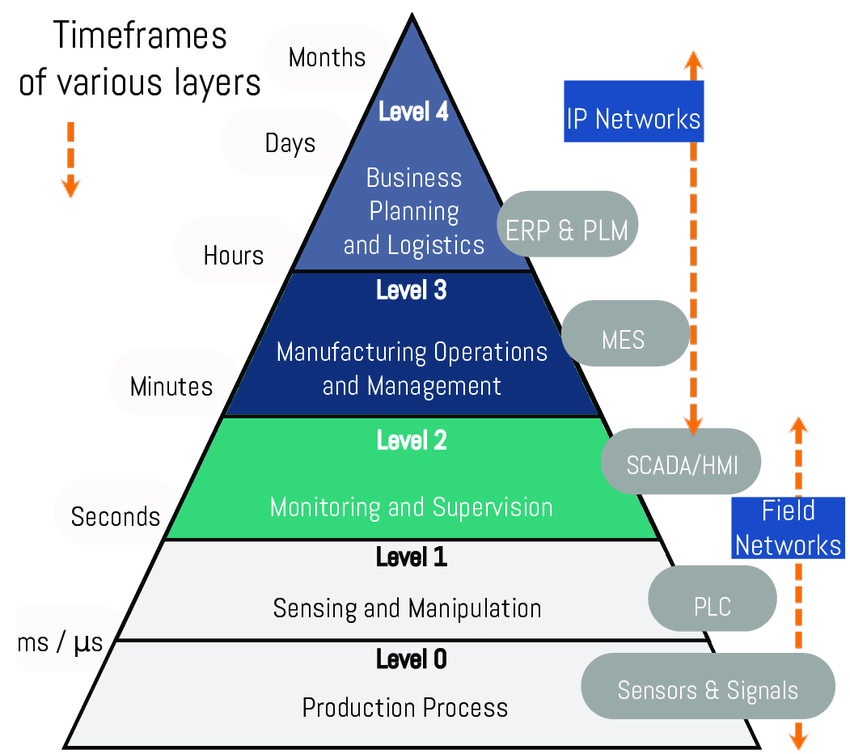
Describing each level thoroughly:
Level 0 - “Production process”: Here is where the actual transformation and production process occurs. Devices such as sensors and actuators automate this process. Data flows in matter of milliseconds or even microseconds.
Level 1- “Sensing and manipulation”: The actuators and sensors of the layer 0 are connected to PLCs. These devices are executing programs continuously which read signals from the sensors and write to actuators. Similar to the previous level, these devices are located next to the machines, therefore are robust.
Level 2 - “Monitoring and supervision”: SCADA system is in the third layer. This acronym means Supervisory Control and Data Acquisition system. This is present when a group of machines with PLCs are connected to another PLC, which monitors and supervise rather than control and process data from other devices like in the level 1. This PLC has an HMI where the user can visualize a control panel. It also enables the user to operate one or multiple machines at the same time in a remote location. This happens in the control room and not necessarily next to the machine in the shop floor.
Level 3 - “Manufacturing operations and management”: Previous levels are highly related to manufacturing functions. In this level, management functions are executed by the planning department. Manufacturing Execution System (MES) software are used to generate production orders, being the instrument for operators from production, logistics and quality departments to know what and when to produce. Information flow in minutes to hours, compared to the previous levels which were in minutes or less.
Level 4 - “Business planning and logistics”: Software applications are Enterprise Resource Planning (ERP) and Product Lifecycle Management (PLM). Information generated and available at this level is used by many departments. Finance and controlling departments can calculate costs, R&D can design and update product features. After-sales can leverage the data for performing installation and maintenance tasks. Even highest level of the organization will use data from here to understand the performance of the organization. Therefore, information time frame can be from days, weeks until months.
Summary
Level description | Type of hardware and software | Time frames of various layers |
---|---|---|
Level 0: Production Process | Sensors and signals | ms/μs |
Level 1: Sensing and Manipulation | PLC | seconds |
Level 2: Monitoring and Supervision | SCADA and HMI | minutes |
Level 3: Manufacturing Operations and Management | MES | hours |
Level 4: Planning and Logistics | ERP and PLM | days, weeks, months |
Outlook
This hierarchical model can generate the following problems:
- Legacy software that can’t communicate with upper layer and/or lower layer. Sometimes manual processes are necessary or non-robust middleware needs to be used.
- Data is siloed, being only available to some departments when it is needed by others located in the same or different location
- Information are over-processed, for example KPIs are calculated several times
- Management needs the information more often and faster to make decisions and information is not ready nor available
Recently, new trends such as Industry 4.0 and the Internet of Things (IoT) have brought new challenges to the automation landscape. As a result, the standard has been updated to ISA-95 Part 2, which includes new concepts such as edge computing and cyber-physical systems.
In summary, the Automation Pyramid is a valuable tool for understanding and communicating about automation systems, but it is important to stay up to date with the latest developments and updates to the standard.
In the following chapters, we will go through each one of these levels and provide detailed examples.
Further materials
If you want to have some more information about the automation pyramid, we can recommend the following two videos: