A typical production line looks like this:
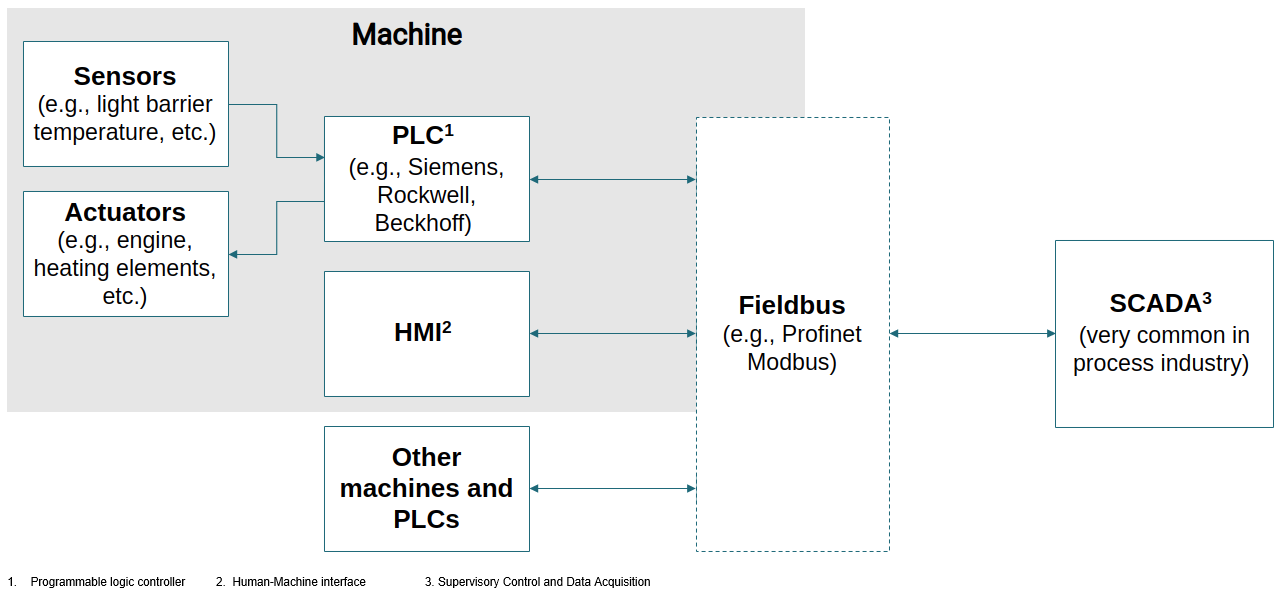
Sensors deliver data to the Programmable Logic Controller (PLC). The PLC is the heart of every modern machine and acts upon the sensor data and sends control signals to the actuators. The actuators then do something, that can be measured again with the sensors. This is called a control loop, and it will keep a process stable, e.g., the temperature in the fridge using a thermometer measuring the temperature, which sends the data to a PLC, which then in turn activates a cooler as an actuator to cool down or stop cooling.
Sometimes it is necessary for the machine operator to interact with the control loop, e.g., to set the target temperature. This is done with a Human Machine Interface (HMI).
A production line might consist out of multiple PLCs, that need to talk with each other. For example, one PLC might want to inform the PLC of the previous machine, that the production was stopped. The previous machine then can stop as well before the buffer between both machines overflows. To communicate between PLCs or PLCs with HMIs, a fieldbus is used.
In process control a production line might consist out of hundreds of machines, and they need to be controlled at the same time. For this, there is a Supervisory Control and Data Acquisition (SCADA) system.